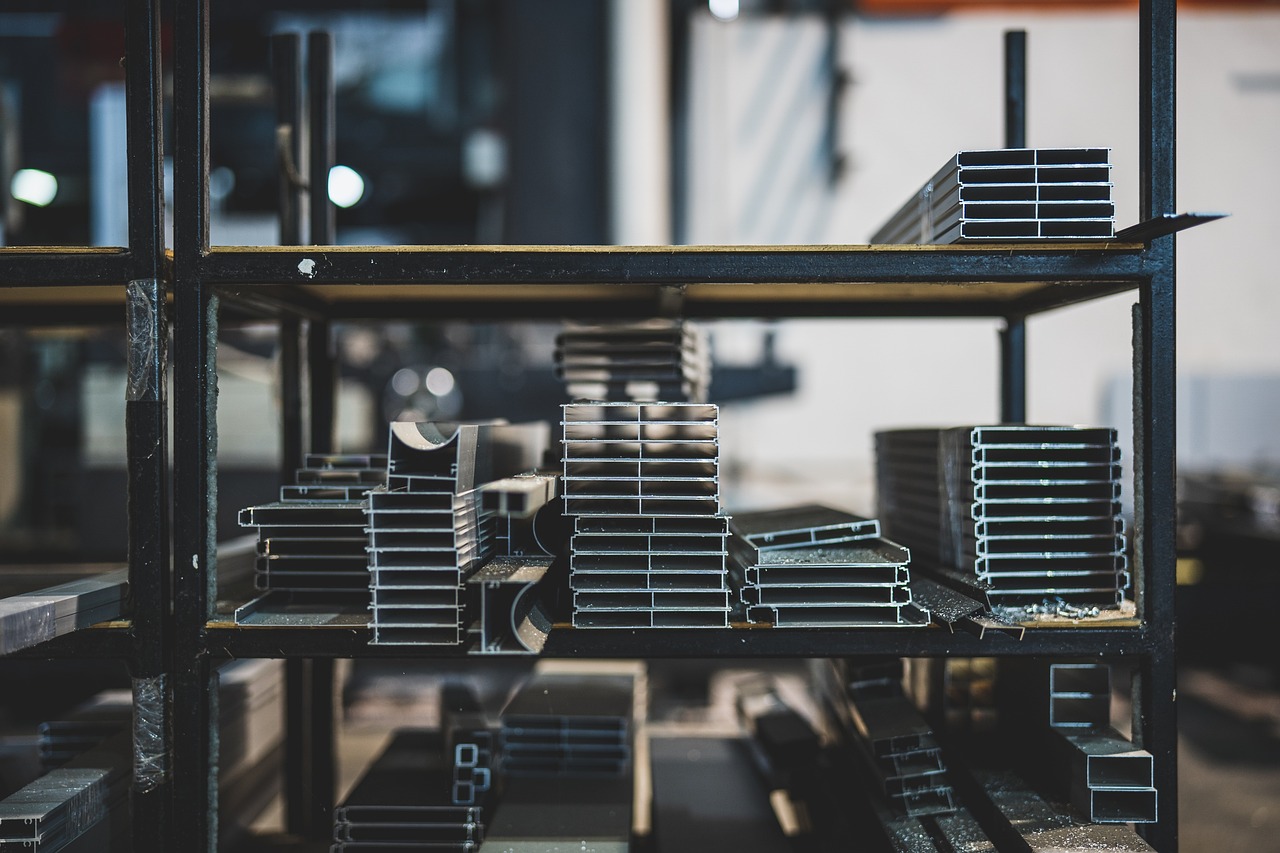
Efficient inventory management is at the heart of any successful warehouse operation. It’s more than just keeping track of what’s on the shelves; it’s about creating systems that make the flow of goods faster, more accurate, and less costly. But how do you turn inventory management into a strength rather than a struggle? In this article, we’ll explore practical strategies that can help businesses improve product storage, management, and shipping, making your warehouse operations smoother and more efficient. Ready to take control?
Start with an Organized Warehouse Layout
A well-organized warehouse is the foundation of effective inventory management. Before diving into software and systems, look at how your space is set up. Are products stored logically, with high-demand items positioned for quick access? Is there enough room for workers to move around safely? Begin by grouping similar items and placing fast-moving products near packing stations to minimize walking time. Clear signage and labels also helps reduce picking errors, making it easier for employees to locate items quickly. An organized layout not only saves time but also reduces confusion, making the entire process more efficient.
Implement Real-Time Inventory Tracking
One of the most impactful improvements you can make is to switch from periodic inventory checks to real-time tracking. Real-time inventory management provides instant updates on stock levels, making it easier to identify low-stock items, monitor incoming shipments, and manage returns. This level of visibility helps prevent stockouts and overstocking—two common pitfalls that can disrupt operations and tie up capital. Use barcode scanning, RFID tags, or other digital tools to keep track of each product’s movement within the warehouse. Not only does this help maintain accurate counts, but it also makes data analysis easier, allowing you to forecast demand and adjust stock levels accordingly.
Adopt the ABC Analysis Method
The ABC analysis is a tried-and-true method for prioritizing inventory based on its value and turnover rate. In this system, ‘A’ items are high-value, fast-moving products that should be monitored and restocked frequently. ‘B’ items have a moderate turnover rate and are less critical, while ‘C’ items are lower in value and slower to move. By categorizing products this way, you can focus your resources on managing the most important inventory first, ensuring that the items generating the most revenue are always available. This approach also helps with space allocation, allowing you to position ‘A’ items for quick access, while ‘C’ items can be stored in less prime areas.
Use Safety Stock Wisely
Safety stock is the extra inventory you keep on hand to cover unexpected demand or supply chain disruptions. While it’s essential to have some safety stock, too much of it can lead to higher storage costs and wasted space. The trick is to find the right balance. Analyze historical sales data, identify patterns, and adjust safety stock levels based on factors like lead time, demand variability, and seasonal trends. The goal is to maintain a cushion that protects against stockouts without tying up excessive resources. Regular reviews are key, as demand patterns can change, requiring adjustments to your safety stock strategy.
Optimize Picking Strategies
Picking is one of the most labor-intensive parts of warehouse management, but it’s also where you can save the most time and resources. There are several picking strategies to choose from, including batch picking, wave picking, and zone picking. Batch picking involves picking multiple orders simultaneously, reducing trips to the same area. Wave-picking groups orders by specific criteria, like shipping deadlines, to optimize efficiency. Zone picking assigns workers to specific areas, so they only focus on products in their zone. The best strategy depends on your warehouse size, order volume, and product variety. Test different methods and refine them based on results, always aiming to reduce travel time and increase accuracy.
Incorporate Palletization for Efficient Storage
Palletization, or the process of stacking products on pallets, is one of the most effective ways to maximize space and improve handling efficiency. Not only does palletization make it easier to move large quantities of goods quickly, but it also simplifies storage and minimizes the risk of damage. By using standard-sized pallets and arranging products logically, you can optimize both storage and transport, making inventory management smoother. Whether it’s for receiving bulk shipments or preparing outgoing orders, palletization is a fundamental technique that supports better space utilization and faster operations.
Leverage Technology for Smarter Inventory Management
Warehouse management software (WMS) is one of the most powerful tools for improving inventory control. A good WMS not only tracks inventory but also provides insights into storage, picking, and shipping processes. Some systems even offer predictive analytics, helping you anticipate demand shifts and adjust stock levels proactively. Consider integrating your WMS with other business systems like ERP or CRM software to create a seamless flow of information. This integration helps you make data-driven decisions, ensuring that your inventory management aligns with broader business goals.
Conclusion: Mastering Inventory Management for Success
Managing inventory effectively isn’t just about keeping shelves stocked—it’s about creating a seamless flow of goods that supports better storage, faster shipping, and greater customer satisfaction. From adopting real-time tracking and the ABC analysis to incorporating palletization and using technology, each step plays a role in building a more efficient warehouse. By following these best practices and continuously refining your strategies, you’ll not only keep your warehouse running smoothly but also support broader business growth.